Core Technologies
2023/02/15
Core Technologies
Okamoto Glass-3 Core competences-
We contribute to our customers by evolving our 3 core technologies:
“Glass Material Development,” “Precision Press Molding Technology,” and “Thin Film Coating Technology”
Glass Material Development
Specialty glass is made by mixing sand, the main raw material, with more than 10 different sub-materials. There are countless possible combinations, and it is said that it is difficult to create new glass even with AI technology. The recipe for glass can only be created through continuous trial and error in selecting raw materials, fine-tuning the composition, melting, and evaluating the glass according to the desired function. The glass recipes are truly the “secret sauce” of the company.
The company’s founder, Mr. Ichitaro Okamoto, was very enthusiastic about the development of new glass. This enthusiasm has been passed down through the generations and has resulted in a wide variety of specialty glass products, including colored glass using advanced coloring technology and high-strength, high-temperature glass.
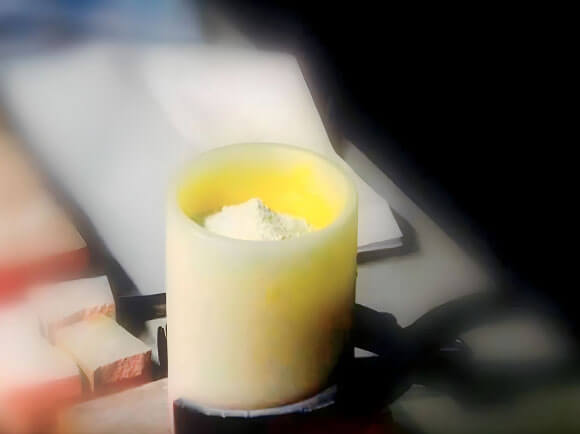
Today, we are evolving this glass material development technology and expanding into the functional glass business, which adds functionality and value to glass. For example, we offer glass materials that can transmit millimeter waves, encapsulating materials that prevent moisture and air from entering, and materials that seal the different types of materials. In addition to glass material technology, we also provide value to our customers through powdering, pasting and sheeting technologies.
Our strength lies in our ability to respond to detailed customer requests such as “I would like to customize the glass frit I am currently using” or “I am looking for a replacement for a discontinued product. We are also available to provide contract manufacturing services for melting, powdering, pasting and sheeting processes.
We develop glass materials for the future, using our expertise and secret glass recipes accumulated over our 90-year history, to provide the service that meets your every need.
Glass frit is available in various forms.
Precision Press Molding Technology
There are various methods of forming glass, such as press molding, blowing, spinning, and casting etc. Okamoto Glass specialize in press molding method. We form glass using a process called “Direct Press Molding”, in which molten glass, which can reach over 1,200°C, is fed into a mold (bottom mold) and pressed with the top and bottom molds. The heat of the molten glass is transferred to the mold, and the glass is formed as it cools and hardens. In this process, it is very important to control the temperature of the mold and the temperature of the glass so that the shape and surface quality of the product are not compromised.
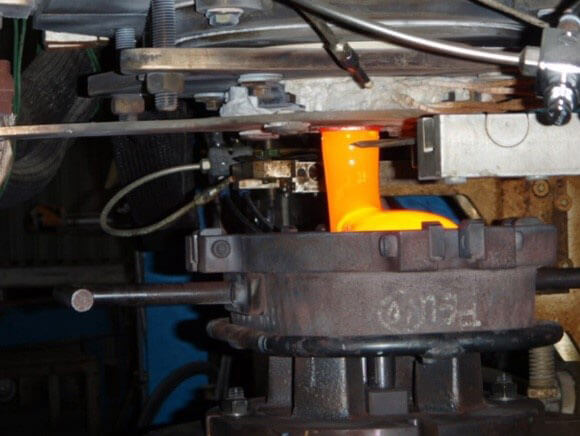
Our strength lies in the technology to precisely control temperatures and adjust various molding conditions that vary from product to product. In addition, our “G-injection®” (glass injection) molding technology, which is an application of direct press molding, makes it possible to form double-sided shapes and complex three-dimensional shapes with glass, which has been difficult with conventional direct presses, by pushing molten glass through the mold at high pressure like plastic injection molding. Another very important factor in the production is the mold. Our glass molding is supported by mold design technology and mold polishing technology. Mold design technology includes the selection of appropriate mold materials, the surface treatment, and calculation of product deformation (shrinkage, etc.) after molding. Mold polishing technology is a craftsman’s art. Craftsmen polish the mold without deforming the microstructure of the mold by sharpening their sense of “hands”, “eyes” and “ears”.
We have two types of melting furnaces: hand (crucibles) furnaces and continuous melting furnaces. The hand furnaces are characterized by its high degree of freedom in the selection of glass materials and molding conditions, as the craftsman can freely roll in the glass melted in the crucible, and are mainly used to produce medium to large-sized products (up to approximately 500mm) such as cover glass for lighting fixtures and washing machines. The continuous melting furnaces have excellent productivity and are suitable for products requiring higher precision, mainly producing reflective mirrors and glass lenses, including fly-eye lenses, aspherical lenses, and irregular-shaped lenses etc., for illumination optical systems.
Okamoto Glass has been a leading manufacturer of direct press molding since its establishment. We will continue to meet the diversifying needs of our customers by developing new technologies to provide even higher precision and quality.
Molded glass products of various sizes.
Thin Film Coating Technology
Vacuum deposition is a thin film formation method in which a metal or oxide is heated and evaporated in a high vacuum and adhered to the surface of a substrate. By alternately depositing films of materials with different refractive indices, it is possible to transmit or reflect the light of any wavelength. This technology is mainly used for optical filters and decorative coatings.
In the latter half of the 1970s, we introduced vacuum deposition technology to add value to glass. Today, the entire Okamoto Group owns more than 40 vacuum deposition machines and offers a variety of products for a wide range of wavelengths from ultraviolet to infrared (200 nm to 10 μm).
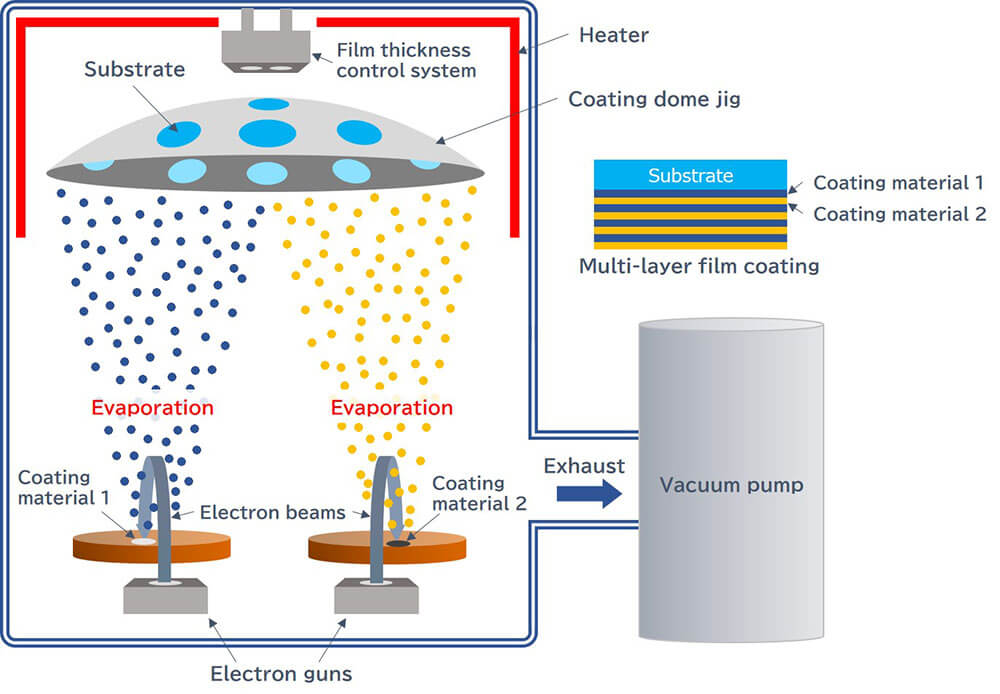
Our strength lies in our technology that applies nanometer-scale thin films uniformly or intentionally non-uniformly to three-dimensional objects such as bowls, curved surfaces, deep shapes, and cylindrical shapes. We utilize this strength mainly for coatings on optical lenses and reflectors, and decorative coatings on cosmetic bottles. We also specialize in thoroughly analyzing the causes of defects and problems, working with customers to find solutions, and proposing optimal improvement plans by using a wide range of equipment such as spectrophotometers, SEM, XRD, ellipsometers, and other analytical instruments, and evaluation equipment such as high temperature and high humidity tests, salt spray tests, and wear resistance tests.
In recent years, we have been actively working with customers on challenging requests and development projects, such as the coating on extremely small shapes and various materials, and developing of new decorative design coatings.
As thin film coating professionals, we continue to explore the possibilities of vacuum deposition. We are committed to providing solutions to customer challenges.
From decorations to optical filters,
we make proposals that are tailored to the customer’s needs.
Other technology
Optical design technology
We support optical design and light distribution simulation. We provide complete support from the optical design stage to the manufacturing of optical components, responding to requests such as “I want a lens that gives this kind of light distribution” or “I want to check the performance of the optical system by simulation” so that we can better realize the optical system that the customer has in mind.